When does an engine fail
When does an engine fail
"Statistically, the first reduction in power after take-off is the most common time for a mechanical failure to occur. Therefore, if a reduced power setting is to be used for the climb, full power should be maintained to a safe height, and the aeroplane cleaned up and established in the climb before power is reduced."
I certainly have seen no evidence to suport the above statement. Given the most common cause of engine failures being Fuel Exhaution/Starvation well after the climb stage.
From these (VH-MYW, VH-MEH, VH-UPY, VH-DAW, VH-FTM, VH-FTM, VH-FEY, VH-HJE, VH-WQA, VH-JQK & VH-NKV) ATSB reports it seems that the Shrike may be the only one that might fall into the first power change after take-off?
I certainly have seen no evidence to suport the above statement. Given the most common cause of engine failures being Fuel Exhaution/Starvation well after the climb stage.
From these (VH-MYW, VH-MEH, VH-UPY, VH-DAW, VH-FTM, VH-FTM, VH-FEY, VH-HJE, VH-WQA, VH-JQK & VH-NKV) ATSB reports it seems that the Shrike may be the only one that might fall into the first power change after take-off?
"Statistically, the first reduction in power after take-off is the most common time for a mechanical failure to occur. Therefore, if a reduced power setting is to be used for the climb, full power should be maintained to a safe height, and the aeroplane cleaned up and established in the climb before power is reduced."
I certainly have seen no evidence to suport the above statement. Given the most common cause of engine failures being Fuel Exhaution/Starvation well after the climb stage.
From these (VH-MYW, VH-MEH, VH-UPY, VH-DAW, VH-FTM, VH-FTM, VH-FEY, VH-HJE, VH-WQA, VH-JQK & VH-NKV) ATSB reports it seems that the Shrike may be the only one that might fall into the first power change after take-off?
I certainly have seen no evidence to suport the above statement. Given the most common cause of engine failures being Fuel Exhaution/Starvation well after the climb stage.
From these (VH-MYW, VH-MEH, VH-UPY, VH-DAW, VH-FTM, VH-FTM, VH-FEY, VH-HJE, VH-WQA, VH-JQK & VH-NKV) ATSB reports it seems that the Shrike may be the only one that might fall into the first power change after take-off?
Also did the engine fail at the power change, or was it the first time the pilot looked inside at the engine gauges to make the power change and notice fluctuations/problems being indicated.
The following 2 users liked this post by 43Inches:
I had an engine failure recently when I pulled back the power on crosswind!
Just a coincidence in my case but does boost the authors stats!
Just a coincidence in my case but does boost the authors stats!
The following users liked this post:
"Statistically, the first reduction in power after take-off is the most common time for a mechanical failure to occur. ... "
I certainly have seen no evidence to suport the above statement. Given the most common cause of engine failures being Fuel Exhaution/Starvation well after the climb stage.
...
I certainly have seen no evidence to suport the above statement. Given the most common cause of engine failures being Fuel Exhaution/Starvation well after the climb stage.
...
Actually, if you read the source document fully, the author seems to make the distinction between mechanical failure and fuel starvation, viz
Fuel contamination
The most probable cause of engine failure is fuel contamination, ie, something in the fuel – most commonly water.
Most students are surprised to learn that mechanical failure is not the most common cause.
...
The most probable cause of engine failure is fuel contamination, ie, something in the fuel – most commonly water.
Most students are surprised to learn that mechanical failure is not the most common cause.
...
Last edited by MickG0105; 30th Jun 2024 at 02:03. Reason: Added point after reading source document
The following 2 users liked this post by MickG0105:
Interesting subject.
I remember a CAA FOI saying the same thing after a CP checkride when I made a safe and legal decision but not a smart one!
Again no idea on the stats but the above stuck with me (nearly 30 years)!
Now I remember a company twin having a failure in cruise, another one on descent, can’t think of any others in 10 years and around 20,000 hours a year.
As for running out of fuel, not a mechanical failure.
I remember a CAA FOI saying the same thing after a CP checkride when I made a safe and legal decision but not a smart one!
Again no idea on the stats but the above stuck with me (nearly 30 years)!
Now I remember a company twin having a failure in cruise, another one on descent, can’t think of any others in 10 years and around 20,000 hours a year.
As for running out of fuel, not a mechanical failure.
The following users liked this post:
"Would fuel exhaustion/starvation be considered a "mechanical failure"?"
Fuel selector failure due broken shaft?
EDP shaft fracture?
Fuel bladder collapse?
Fuel hose internal collapse?
Fuel hose becomes a Pope Srinkler?
Mixture lever bolt falls out?
Compounding error due fuel gauge error over time, whe tanks are not often filled?
Fuel cap incorrect fitment?
Fuel strainer falls off?
These can all cause the engine to fail & are mechanical. They all caused the engine to stop - but none were at a first power change after take-off.
Fuel selector failure due broken shaft?
EDP shaft fracture?
Fuel bladder collapse?
Fuel hose internal collapse?
Fuel hose becomes a Pope Srinkler?
Mixture lever bolt falls out?
Compounding error due fuel gauge error over time, whe tanks are not often filled?
Fuel cap incorrect fitment?
Fuel strainer falls off?
These can all cause the engine to fail & are mechanical. They all caused the engine to stop - but none were at a first power change after take-off.
The following users liked this post:
engine failures
Another article on engine failures quotes FAA but doesn't give a reference.
https://www.twinandturbine.com/stati...ston%20engines.
and one on cause of failures
https://www.aviationsafetymagazine.com/features/why-engines-fail/
SB
https://www.twinandturbine.com/stati...ston%20engines.
and one on cause of failures
https://www.aviationsafetymagazine.com/features/why-engines-fail/
SB
It’s also something I used to abide by and to this day when flying a piston twin, I never touch anything before at least 500’ AGL and then it’s usually just to bring the RPM back somewhat. Everything else is left until I’m climbing through 4,000’.
Having said that, these days I’m more inclined to think that most failures occur in the cruise for the simple reason that that’s where everyone probably spends 95% of their time when in the aeroplane.
I've never seen any real evidence to suggest otherwise (actual statistics or anything else).
The following users liked this post:
It's one of those statements that had its origins in the old days when huge numbers of piston engined warplane operations and post-WWII GA/airline aircraft operations included fiddling with the throttle and the prop setting soon after take off as SOP (which persists with e.g. the 25"/2500 RPM practice). Old mate 'Bend alot' has (as usual) conflated and confused concepts that are more properly expressed as Venn Diagrams. A mechanical failure doesn't necessarily equate to an engine failure or no more motion lotion delivered to the engine.
The failure of a propellor governing system component is a mechanical failure which does not usually cause "engine failure". It might cause e.g. a temporary overspeed, but that's not going to cause a loss of engine thrust. All those historic failures of propellor governing systems is the source of all the mainly-pointless pre-takeoff 'exercising' of modern CSUs - sometimes twice but - heck - let's make it three or four times for extra 'safety' by maximising the risk of rocks and other crap damaging the blade leading edges.
So best to track down primary authority for the "mechanical failure" data to which Bendy's quote refers.
And track down some data about the number of times an 'ordinary' CSU fitted to an 'ordinary' GA aircraft in the last - pluck 20 years - has been found to have been malfunctioning during one of those pre-flight 'exercises' or shortly after take-off and RPM reduction.
The failure of a propellor governing system component is a mechanical failure which does not usually cause "engine failure". It might cause e.g. a temporary overspeed, but that's not going to cause a loss of engine thrust. All those historic failures of propellor governing systems is the source of all the mainly-pointless pre-takeoff 'exercising' of modern CSUs - sometimes twice but - heck - let's make it three or four times for extra 'safety' by maximising the risk of rocks and other crap damaging the blade leading edges.
So best to track down primary authority for the "mechanical failure" data to which Bendy's quote refers.
And track down some data about the number of times an 'ordinary' CSU fitted to an 'ordinary' GA aircraft in the last - pluck 20 years - has been found to have been malfunctioning during one of those pre-flight 'exercises' or shortly after take-off and RPM reduction.
Last edited by Lead Balloon; 30th Jun 2024 at 09:28.
The following 2 users liked this post by Lead Balloon:
It's one of those statements that had its origins in the old days when huge numbers of piston engined warplane operations and post-WWII GA/airline aircraft operations included fiddling with the throttle and the prop setting soon after take off as SOP (which persists with e.g. the 25"/2500 RPM practice). Old mate 'Bend alot' has (as usual) conflated and confused concepts that are more properly expressed as Venn Diagrams. A mechanical failure doesn't necessarily equate to an engine failure or no more motion lotion delivered to the engine.
The failure of a propellor governing system component is a mechanical failure which does not usually cause "engine failure". It might cause e.g. a temporary overspeed, but that's not going to cause a loss of engine thrust. All those historic failures of propellor governing systems is the source of all the mainly-pointless pre-takeoff 'exercising' of modern CSUs - sometimes twice but - heck - let's make it three or four times for extra 'safety' by maximising the risk of rocks and other crap damaging the blade leading edges.
So best to track down primary authority for the "mechanical failure" data to which Bendy's quote refers.
The failure of a propellor governing system component is a mechanical failure which does not usually cause "engine failure". It might cause e.g. a temporary overspeed, but that's not going to cause a loss of engine thrust. All those historic failures of propellor governing systems is the source of all the mainly-pointless pre-takeoff 'exercising' of modern CSUs - sometimes twice but - heck - let's make it three or four times for extra 'safety' by maximising the risk of rocks and other crap damaging the blade leading edges.
So best to track down primary authority for the "mechanical failure" data to which Bendy's quote refers.
I think that your claim of war time aircraft on engine failure is possible the source.
The following 2 users liked this post by Bend alot:
Join Date: Jun 2000
Posts: 473
Likes: 0
Received 0 Likes
on
0 Posts
Me too 421 dog but mine was on rotate on a field limiting strip
Bitch of an engine if not well treated on both the 404 and the 421 (cracked front pots more often than not)
Descent/Power reduction profile ....you needed to me a mathematician
From memory our company proceedure was 1 inch boost per min starting 2 min from TOD
Push the nose over and then another min before taking off another inch of boost then reduce 1 inch per 3000 feet of descent
Having flown these engines for some 5 years back in the 90's it was always drummed into us that an engine rarely failed when in equilibrium so any power reduction must be done slowly to reduce the rate of change in balance of forces....to the extent that the pax should barely percieve a change of engine note.
Interested your input ref your power reduction
Closing in on 15,000 hrs TT and I’ve had two engine failures in a light twin:
So one at take off power and one at probably 55% Econ.
So I’m at 50/50.
Nothing since I’ve moved on to jets.
- On take off at 400’
- In a hold at 7000’
So one at take off power and one at probably 55% Econ.
So I’m at 50/50.
Nothing since I’ve moved on to jets.
The following users liked this post:
40 years 21000 hours
No jet engine failures or shut downs
No Piston engine failures
2 turbo prop failures one catastrophic and one flame out fuel control unit issue
2 turbo prop precautionary shutdowns, both oil pressure related issues.
Never on Takeoff
3 in the cruise above 10000ft
1 flameout on approach to land.
1 electronic propellor control failure, no shutdown required
1 loss of hydraulic fluid requiring alternate gear extention, stop on runway and towed to the gate. plenty of notice and preplanning enroute.
No jet engine failures or shut downs
No Piston engine failures
2 turbo prop failures one catastrophic and one flame out fuel control unit issue
2 turbo prop precautionary shutdowns, both oil pressure related issues.
Never on Takeoff
3 in the cruise above 10000ft
1 flameout on approach to land.
1 electronic propellor control failure, no shutdown required
1 loss of hydraulic fluid requiring alternate gear extention, stop on runway and towed to the gate. plenty of notice and preplanning enroute.
The following users liked this post:
GTSIO 520M
Me too 421 dog but mine was on rotate on a field limiting strip
Bitch of an engine if not well treated on both the 404 and the 421 (cracked front pots more often than not)
Descent/Power reduction profile ....you needed to me a mathematician
From memory our company proceedure was 1 inch boost per min starting 2 min from TOD
Push the nose over and then another min before taking off another inch of boost then reduce 1 inch per 3000 feet of descent
Having flown these engines for some 5 years back in the 90's it was always drummed into us that an engine rarely failed when in equilibrium so any power reduction must be done slowly to reduce the rate of change in balance of forces....to the extent that the pax should barely percieve a change of engine note.
Interested your input ref your power reduction
Me too 421 dog but mine was on rotate on a field limiting strip
Bitch of an engine if not well treated on both the 404 and the 421 (cracked front pots more often than not)
Descent/Power reduction profile ....you needed to me a mathematician
From memory our company proceedure was 1 inch boost per min starting 2 min from TOD
Push the nose over and then another min before taking off another inch of boost then reduce 1 inch per 3000 feet of descent
Having flown these engines for some 5 years back in the 90's it was always drummed into us that an engine rarely failed when in equilibrium so any power reduction must be done slowly to reduce the rate of change in balance of forces....to the extent that the pax should barely percieve a change of engine note.
Interested your input ref your power reduction
This failure was a one off. I actually thought I had just blown up the turbo, because I lost boost but not oil pressure. I shut it down within 10-15 seconds and landed at a pretty substantial airport (which was probably also the “first appropriate”) I had 7 qts of oil at landing (generally fly with 11) When I got on the ground and actually saw what happened, the left #6 piston was laying in the nacelle having broken the wrist pin and subsequently being driven into the head, which subsequently broke the cylinder in half and broke off the corresponding intake and exhaust connections (I couldn’t see any of this while in flight of course, because the port side of the port cowling took the hit.
When I sent it out for rebuild, the propshaft (bull gear) which is how most GTSIOs fail, (because it’s a bendix gear and really doesn’t like reverse torque) was perfect.
I asked Textron if they wanted to stand behind it because the wrist pin was almost certainly defective, but they said that since the engine was more than 12 years old, it wasn’t in compliance with their service letter requiring replacement at TBO or 12 years, tough luck.
421’s have enough power that they fly just fine on one engine (even if you lose the critical), with little more than easy climb settings on the good mill.
I’ve had a couple of 421’s, and love them for my typical 1-3 hr missions. I have shut down a few engines but always for minor issues that appeared to be possiblely engine threatening at the time, but ended up being no big deal.This is the only time I actually had one break…
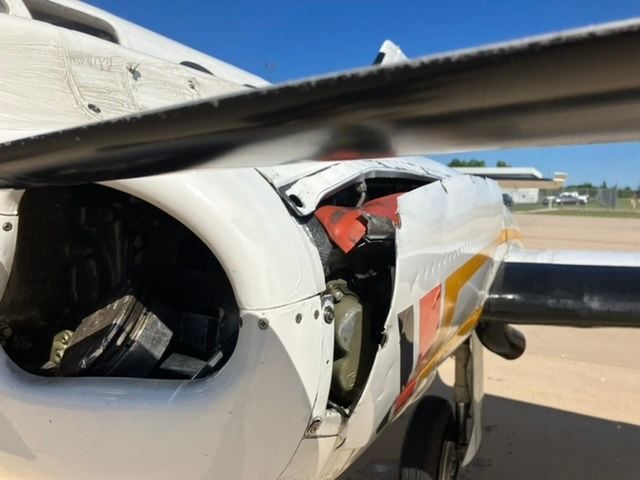
Last edited by 421dog; 1st Jul 2024 at 00:32.
Man Bilong Balus long PNG
Join Date: Apr 2002
Location: Back in Japan, flying the Glider Tug, eating great Japanese food, looking at lovely Japanese Ladies and continuing the neverending search for a bad bottle of Red.
Posts: 2,984
Received 111 Likes
on
64 Posts
"Statistically, the first reduction in power after take-off is the most common time for a mechanical failure to occur.
Had one genuine engine failure back in my PNG days. Took off from Kamulai in a BN2 and climbed up to around 9,000` to head back to Port Moresby. After about 10 or so minutes in the cruise, the RH engine started running very roughly. Looked at Oil pressure gauge and it read zero! Then looked at the Engine itself and oil was streaming down the fairing on the landing gear so I shut the engine down, and informed Flight Service (Remember them? We used to have one

Upon arrival at Port Moresby, I thanked the Tower for the `Welcoming Committee` (Fire trucks etc) and managed to taxi to Yorky Mendoza`s Maintenance Hangar. As soon as I shut down the remaining engine his Engineers pounced on the A/C.
When they removed the bottom engine cowl, there was a loud `CLUNK` and one entire cylinder, with piston still inside it, fell to the ground and rolled around on the tarmac!

The senior LAME took me aside shortly afterwards and quietly told me that the LH Engine did not sound all that good to him when I came in!

AFAIK, that particular Bongo Van never flew again!