Alaska Airlines 737-900 MAX loses a door in-flight out of PDX
It is not made mostly of carbon fibre but aluminium.
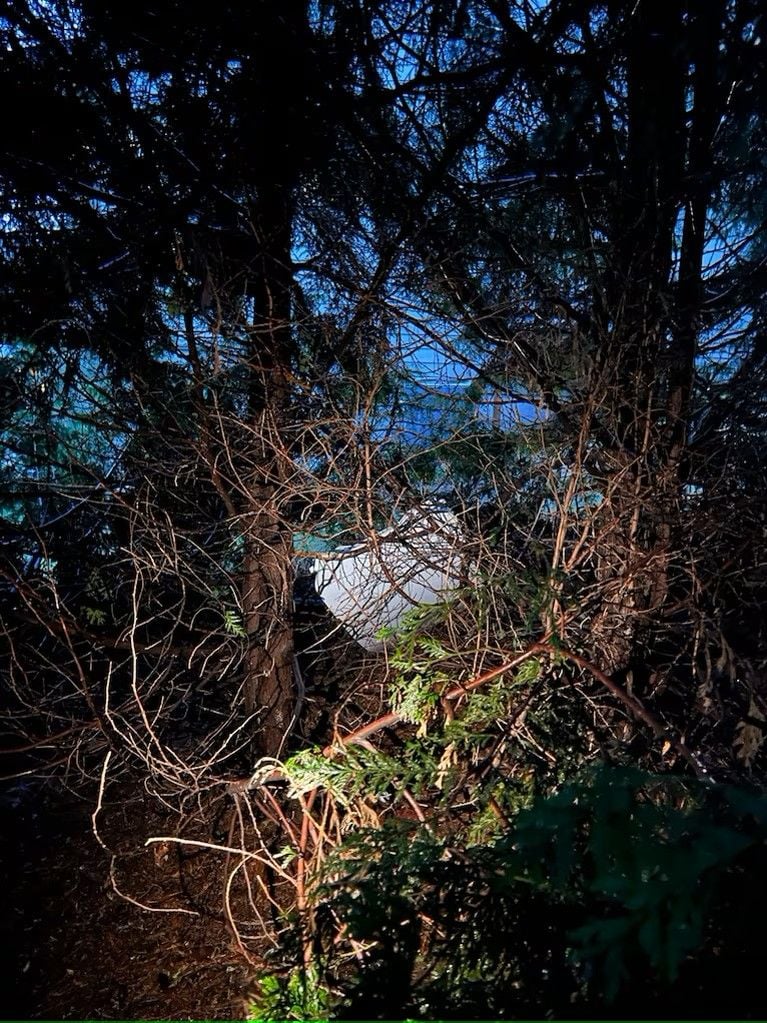
I think the one in your post is where it was moved to after being found.
And if you look at the bottom of the plug, the aft hinge assembly apparently put up a little fight, and the forward one not as much. You can note the aft, lower inner frame is bent outwards from contact with the aft hinge pin assembly, and some of the outer paint is rubbed through to the zinc chromate layer underneath (inside blue circle). Or it at least looks like abrasion in the low-res photo, and not paint popping off from deformation.
I don’t think that could cause an issue between the skin and the frame - the yellow arrow shows the restraining cable attachment, via that ring to the frame. Looks like the cable parted at the door end, which was connected to the frame.
So both aft connection points did not let go cleanly, but were forced - 1) the forced upper guide track and 2) the bent lower hinge area. I’m sure the NTSB people already know how this happened, with access to the whole unit and ability to examine the whole assembly, bolt holes, etc.
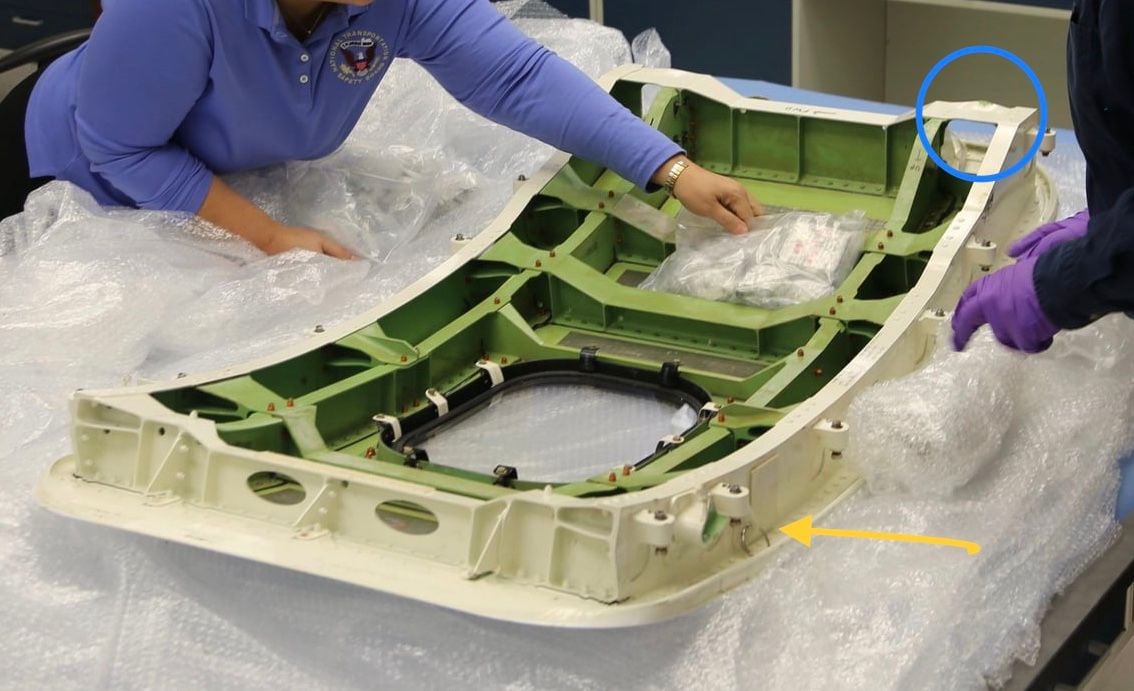
So both aft connection points did not let go cleanly, but were forced - 1) the forced upper guide track and 2) the bent lower hinge area. I’m sure the NTSB people already know how this happened, with access to the whole unit and ability to examine the whole assembly, bolt holes, etc.
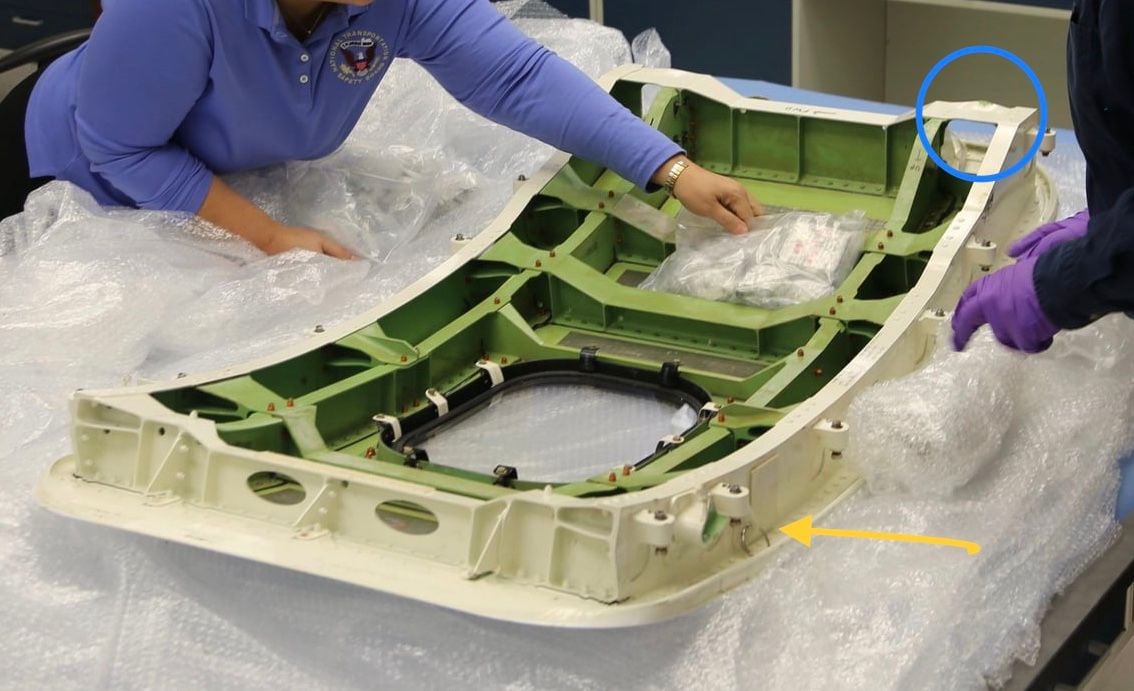
Join Date: Jun 2009
Location: Montreal
Age: 65
Posts: 41
Likes: 0
Received 0 Likes
on
0 Posts
One thing the NTSB lab photo shows, I think, is that the lower hinge post guide fittings are attached to the door with one-lug nutplates. You can see them beside the NTSB lady's arm.
Something like MS21061. It's interesting because the places I've worked usually avoid one-lug nut plates when possible due to the risk of attachment rivet breakage. Non-trivial disassembly of structure is usually required to replace them.
Something like MS21061. It's interesting because the places I've worked usually avoid one-lug nut plates when possible due to the risk of attachment rivet breakage. Non-trivial disassembly of structure is usually required to replace them.
Difficult to see but…
Fractured was word used by Mrs H early on for the top guides… photo not good quality, but looks a bit more like folded open… was not much flesh on the bracket there in the first place…
scenario option … 14,830ft 271kt 14.09psi.. top opens up …press 11.64 psi…plug caught be airflow opens wider, rips steel wire… 15,859ft 271kt 9.08psi … plug flips 90 deg down, then ripped off, … low hinges departure prevents plug from hitting the horizontal stabiliser …
forward (in DOF) hinge stripped, aft hinge ripped,
scenario option … 14,830ft 271kt 14.09psi.. top opens up …press 11.64 psi…plug caught be airflow opens wider, rips steel wire… 15,859ft 271kt 9.08psi … plug flips 90 deg down, then ripped off, … low hinges departure prevents plug from hitting the horizontal stabiliser …
forward (in DOF) hinge stripped, aft hinge ripped,
Join Date: Mar 2019
Location: Bavaria
Posts: 20
Likes: 0
Received 0 Likes
on
0 Posts
Why does the door plug look overdesigned, with heavy machinged members? The main reason is because it works as a curved plate to carry the pressure, which means there is a lot of plate bending in the structure. Baseline fuselage structure works as a pessure vessel with primary loads in tension. Plate bending is structurally inefficient.
Why don't they bolt together the stop pads and stop fittings? That's because it would change the load paths. Doors are designed not to pick up general fuselage loads, they sort of "float". So if you created bolted connections to the fuselage at 12 points, the door would become primary structure and you would have to redesign local fuselage frames, intercostals, and skins, and add a nontrivial certification item to cover just the plug doors. For design, analysis, and testing, you are potentially looking at 7 figures.
Why don't they bolt together the stop pads and stop fittings? That's because it would change the load paths. Doors are designed not to pick up general fuselage loads, they sort of "float". So if you created bolted connections to the fuselage at 12 points, the door would become primary structure and you would have to redesign local fuselage frames, intercostals, and skins, and add a nontrivial certification item to cover just the plug doors. For design, analysis, and testing, you are potentially looking at 7 figures.
The tension in the fuselage (along the circumference) will expand the doorframe, increasing the distance between roller pin and hinges.
Bending of the door will do the opposite to the upper guide track and hinge brackets.
If there is not enough play in the bolts and roller guide (remember the slotted holes on the hinge brackets which allow adjustment), the plug will take over fuselage tension due to pressure differential.
If this tension is strong enough to break/shear the lower bolts, stored energy may just be enough to snap the plug up off the lower pads and/or break the upper bolts or guide track.
Just another theory which would imply wrong adjustment (or design), not missing parts. But it somehow fits to the pictures so far.
This failure mode would be unique to the plugs, not applicable to the emergency doors. The 'real' emergency door design does not limit the 'floating' of the door on the pads as the plug does since the hinges are not blocked. Four bolts in all four corners on the plug counteract the intention of having the door/plug float on pads and decoupling it from the fuselage tension. Maybe they accidentially bolted the plug in the fuselage tension load path trying to have redundancy on the bolts.
Is there any difference in fuselage stiffness between NG/ER/MAX versions equipped with plugs? Could this be a contributing factor?
Are those loose nuts on the other planes really loose or did excessive tension stretch the screws, actually preventing further accidents?
I hope they will find the right answer.
Boeing was really, really bad at building airplanes
Without learning, history will repeat;
"Boeing was really, really bad at building airplanes"
https://valkstrat.com/the-myth-of-old-boeing/
"Boeing was really, really bad at building airplanes"
https://valkstrat.com/the-myth-of-old-boeing/
I wonder when "UP" and FWD" with corresponding arrows were marked on the door plug. Would those marking have been required for production assembly or only for someone unfamiliar with how the plug was fitted.
"Up" and "Fwd"


Join Date: Jan 2024
Location: Sri Lanka
Posts: 4
Likes: 0
Received 0 Likes
on
0 Posts
Pressure test after WIFI install
After installing WIFI antenna they must have done a pressure test of the cabin . After that the Warnings from the pressure systems started . What if the test moved or damaged something in the door plug . It has happened before on a Boeing in Oklahoma City that too much pressure during test caused big cracks in the fuselage . USAF KC-135. In 1999 .
Last edited by retiredCSE; 16th Jan 2024 at 06:11. Reason: spelling correction , wrong plane model
Join Date: Jun 2000
Location: Chicago
Posts: 55
Likes: 0
Received 0 Likes
on
0 Posts
One thing the NTSB lab photo shows, I think, is that the lower hinge post guide fittings are attached to the door with one-lug nutplates. You can see them beside the NTSB lady's arm.
Something like MS21061. It's interesting because the places I've worked usually avoid one-lug nut plates when possible due to the risk of attachment rivet breakage. Non-trivial disassembly of structure is usually required to replace them.
Something like MS21061. It's interesting because the places I've worked usually avoid one-lug nut plates when possible due to the risk of attachment rivet breakage. Non-trivial disassembly of structure is usually required to replace them.
We still cant explain the missing fwd guide. The easiest explanation: it was never there.
The fasteners would have been subject to shear loads rather than tension loads. This would have put the screws against the sides of the holes in the door. If they are replaceable element nut plates, the float of the nut plates would isolate the nutplate rivets from load. They may even have just turned with the rivet as the pivot to allow that contact.
Join Date: Jun 2000
Location: Chicago
Posts: 55
Likes: 0
Received 0 Likes
on
0 Posts
Whilst having the bottom of the door plug move out would explain the separation of the skin at the top it is hard to see how the bottom could have moved out first. The two shafts remain attached and the rear bracket mounting bolts appear to have been broken by considerable force suggesting the rear bracket at least was correctly in place (though probably not with a lock bolt).
The damages on the bottom rib are when the hinges were ripped out of the plug. It appears to me, they didnt pull straight out cleanly, but rather the plug was released bottom first, and pivoted on the top guides perhaps 10 degrees, which caused the bottom hinges to be removed violently against the rib structure. (It is this chain of events which dictated whether the plug went around, or straight into the H.Stab)

Join Date: Mar 2019
Location: Boston
Posts: 2
Likes: 0
Received 0 Likes
on
0 Posts
Witness marks on the frame/fuselage skin?
If the bottom of the plug pivoted out, causing the top of the plug skin to hit against the opening at the top and causing the observed separation damage in the lab photo, would there not be witness marks on the the top of the plug door frame/fuselage skin? Are there any good pictures of the outside of the plane at the top of the opening?
Join Date: Jan 2024
Location: Copenhagen
Posts: 16
Likes: 0
Received 0 Likes
on
0 Posts
missing locking compound?
When comparing the picture from the NTSC lab to a Seattle Times entry "Boeing and U.S. aerospace set back by Alaska Airlines fuselage blowout" (I am not allowed to include URL, sorry) then I observe on the ST picture that all of the bolts are locked with a green locking compound, including the 12 studs. This I cannot find on the studs of the plug at the NTSC lab. I do as well miss the hole for the locking bolt in the guide track. Is it hidden due to warping of the of the guide track?

Join Date: Mar 2016
Location: San Diego
Posts: 4
Likes: 0
Received 0 Likes
on
0 Posts
There are witness marks on the stop pads from the door resting on them. Could be damage from the departure but could also be rub marks over a longer period.
I think the door first went up a bit and the pins were no longer resting against the stop pads but the flange that holds the stop pins. During that period, there were probably leaks around the door which would explain the pressure system detecting fluctuations.
The question arises then if it would have been possible to see the plug sticking out a quarter inch during that time which might have been days / weeks. It would have been up half an inch as well.
I think the door first went up a bit and the pins were no longer resting against the stop pads but the flange that holds the stop pins. During that period, there were probably leaks around the door which would explain the pressure system detecting fluctuations.
The question arises then if it would have been possible to see the plug sticking out a quarter inch during that time which might have been days / weeks. It would have been up half an inch as well.
Without learning, history will repeat;
"Boeing was really, really bad at building airplanes"
https://valkstrat.com/the-myth-of-old-boeing/
"Boeing was really, really bad at building airplanes"
https://valkstrat.com/the-myth-of-old-boeing/
Any system that is working well to fulfill the above is doing its job better than one that is newer and more efficient but less good at fulfilling key needs.
Replacing old but tried and true processes in commercial aerospace is hard to do right. It might seem right from a financial and ability perspective, but those are not what keep large, deliberate aerospace enterprises running successfully.
Boeing would be better off with a corporate structure that has no shareholders.